With the advancement of the plastics recycling economy, more and more plastics companies are working to improve the recyclability of plastics to cope with waste plastics and promote the sustainable development of the plastics industry.
In a December 2018 study, McKinsey & Company confirmed the enormous potential of chemical recycling: if existing recycling processes are combined with new processes such as chemical recycling, experts believe that by 2030, global plastic recycling The rate is expected to be 50% from the current 16%. The proportion of chemical recovery may rise from the current 1% to around 17%, equivalent to about 74 million tons of plastic waste.
The development potential of chemical recycling is considerable, and it can be described as one of the innovative solutions for the sustainable development of plastics. Therefore, some major chemical brands have also begun to invest in the research and development of chemical recycling processes and achieved initial results.
Dow: Using innovative chemical recycling to use at least 100,000 tons of recycled plastic by 2025!
Dow has announced that it is working with the Dutch chemical company Fuenix Ecogy Group to convert waste plastics into pyrolysis oils to expand waste plastic recycling and address the growing global waste plastic pollution problem.
The Fuenix Ecogy Group has developed a plastics decomposition technology that converts waste plastic into a new type of pyrolysis oil for recycling.
Dow said it plans to implement the process at its plant in Terneuzen, the Netherlands, as a recycling process.
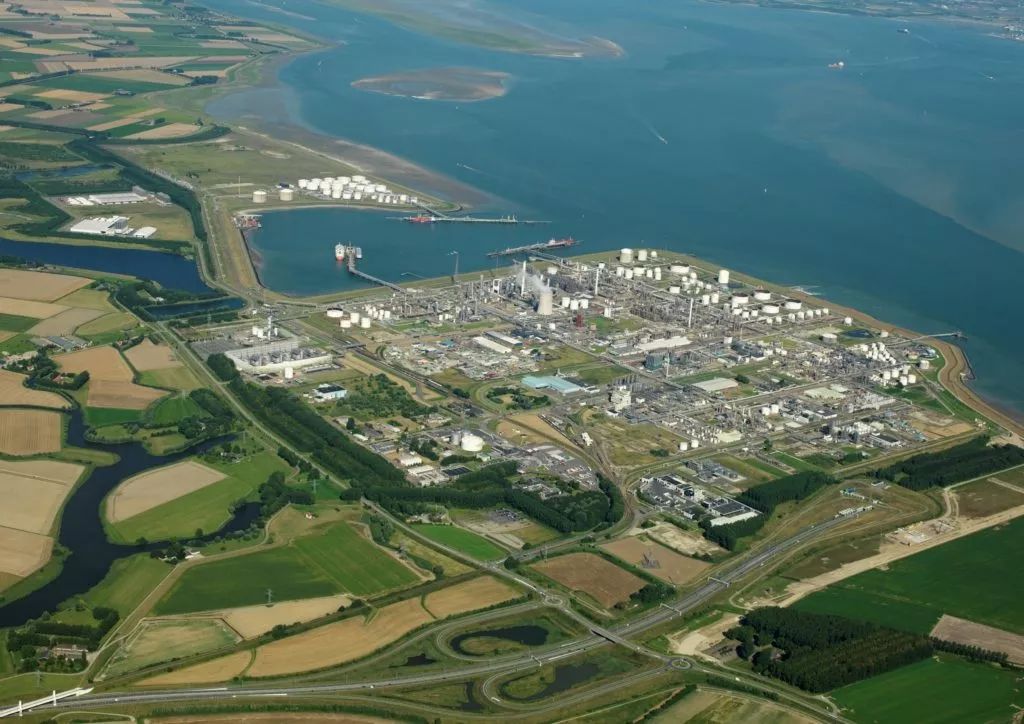
Dow's production site in Terneuzen, The Netherlands.
Chemical companies face the problem of solving waste plastic pollution that destroys global marine life and ecosystems.
Retail and consumer giants including Unilever, Wal-Mart, Coca-Cola, etc. have pledged to increase the use of recycled plastics, creating a market value of approximately $120 billion in Canada and the United States alone. The lack of cost-effective recycling processes has always been one of the biggest obstacles.
Breakthrough technology: recycling for wider application
According to a report by Closed Loop Partners, an investment company focused on saving economic resources, at least 60 companies are researching recycling solutions and investing in rapid scale.
Most plastics sent to the world are not recycled, and nearly 90% of plastic waste eventually enters landfills, incinerators, rivers and oceans. According to reports, in the United States and Canada, only about 6% of plastics can be recycled.
According to Dow, Fuenix's technology is a more flexible solution than traditional physical recycling methods that only recycle limited plastic applications.
The product of this process, known as pyrolysis oil, is suitable for the manufacture of food packaging and medical products, which typically require the production of nascent plastic materials such as crude oil.
It is reported that the plastics produced by the pyrolysis oil produced by the new process are comparable to those made of crude oil. Fuenix has developed this technology over the past seven years and has focused on recycling plastics that cannot be reused or recycled. And the practice of most companies with similar processes is to convert plastic waste into fuel.
Fuenix chemical recycling process.
<PLASTIC RECYCLING SOLUTION , http://www.get-recycling.com/>
<PET RECYCLING , http://www.get-recycling.com/solutions_show.asp?id=12 >
<HDPE PP RECYCLING , http://www.get-recycling.com/solutions_show.asp?id=11>
The company said that by 2025, the cooperation will help Dow use at least 100,000 tons of recycled plastics to make products and enter the EU market. As early as 2021, the European Union began to ban the use of disposable plastic tableware, such as dishes, forks and straws, to reduce marine waste.
Fuenix says the technology can reduce CO2 emissions by 65% compared to methods such as incineration and energy recovery.
The method may be able to enter the vast plastics market and have the opportunity to share a share of the petroleum product market. “The vast majority of mechanically recycled plastics cannot do this,” said Maarten Bakker, professor of resources and recycling at Delft University of Technology in the Netherlands.
“This is a promising technology for some waste streams that cannot be mechanically recycled now,” he added.
In addition to Dow, many companies are also committed to promoting innovative recycling processes and promoting the development of plastic recycling economy.
BASF: Chemical cycle projects are beginning to bear fruit
BASF is advancing the chemical cycle project to help the circular economy. At the end of 2018, BASF used pyrolysis oil extracted from plastic waste as its raw material for the first time in its production.
At the recent press conference of the K 2019 exhibition in Düsseldorf, Germany, BASF and its partners Jaguar, Storoco and Schneider Electric demonstrated the initial results of the pilot phase of the chemical cycle project.
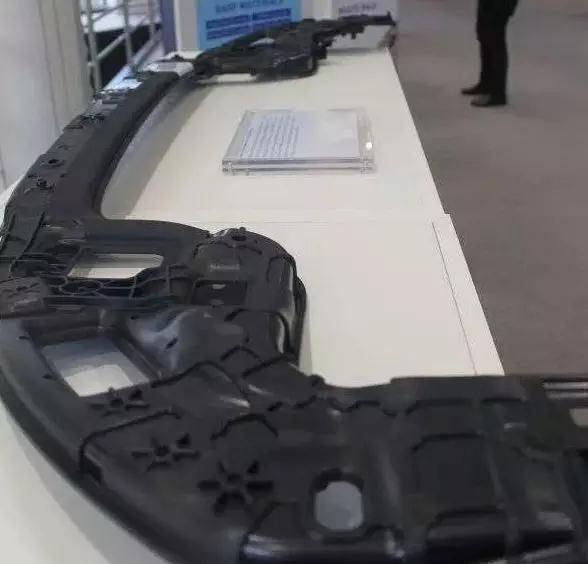
For example, the Jaguar Land Rover (JLR) developed a prototype of a plastic front-end bracket for its first electric SUV, the i-Pace. This plastic front bracket is made of BASF's recycled plastic Ultramid® B3WG6 Ccycled Black 00564.
Craig Woodburn, Jaguar Land Rover Global Environmental Compliance Manager, said:
"
As part of our accelerated closed-loop manufacturing operations, we are always looking for advanced technologies that reduce waste of resources. The BASF Chemical Cycle project transforms post-consumer plastic waste into safe, quality-assured parts, an important step in moving us towards zero waste.”
Through the "ChemCycling", BASF has opened up a whole new field of recycling plastic waste. Depending on the region, these plastic wastes are usually sent to landfills or burned for energy recovery. But chemical cycles are another option: through thermochemical processes, these plastics can be used to produce syngas or oil. The resulting recycled feedstock can replace some fossil resources for the production of BASF related products.
SABIC: Production of certified cyclic polymers using a chemical recycling process
At K 2019, Saudi Basic Industries Corporation (SABIC) will focus on the “Making a World of Difference Together”, focusing on the synergy of industry chains created for sustainable development.
Among them, the certified circulating polymer produced by the use of pyrolysis oil raw materials for the recovery of mixed plastic waste will be one of the highlights of many exhibitions.
It is reported that SABIC is using raw materials made from mixed plastic waste at the Geleen production site in the Netherlands to produce certified recycled polymers.
At K 2019, Saudi Basic Industries Corporation (SABIC) highlighted the synergy of industry chains created to achieve sustainable development.
SABIC intends to build a semi-commercial plant dedicated to the improvement and upgrading of pyrolysis oil feedstock, which is expected to be put into commercial production in 2021.
As a disruptive innovation, SABIC has introduced certified cyclic polymers designed to change the entire value chain.
This recycled polymer requires SABIC to collaborate with its upstream and downstream suppliers and customers to produce high-quality recycled plastic waste and then use it as a raw polymer for high-quality applications to recycle the Earth's natural resources.
Certified recycled polymers will first be supplied to leading brand customers, including Unilever, Tupperware, Vinventions and Walki Group, for the development of advanced high quality consumer products or packaging for food, beverage and personal care products.
Frank Kuijpers, General Manager, SABIC Sustainability.
<PLASTIC RECYCLING SOLUTION , http://www.get-recycling.com/>
<PET RECYCLING , http://www.get-recycling.com/solutions_show.asp?id=12 >
<HDPE PP RECYCLING , http://www.get-recycling.com/solutions_show.asp?id=11>